
Electronics Housing Injection Molding Services
Protoshop Inc. provides personalized solutions for our clients’ projects. We specialize in crafting precision-engineered injection-molded prototype parts for various applications, including electronic housings.
Electronic housings safeguard sensitive components within electronic devices. Housings shield these components from environmental factors like dust, moisture, and temperature fluctuations, ensuring the devices’ functionality and reliability over time.
Housings also provide a protective, tamper-resistant enclosure to prevent damage to internal electronic components, prolonging the device’s lifespan. This is particularly important in industries where durable and long-lasting electronic equipment is crucial, such as aerospace, automotive, and medical.
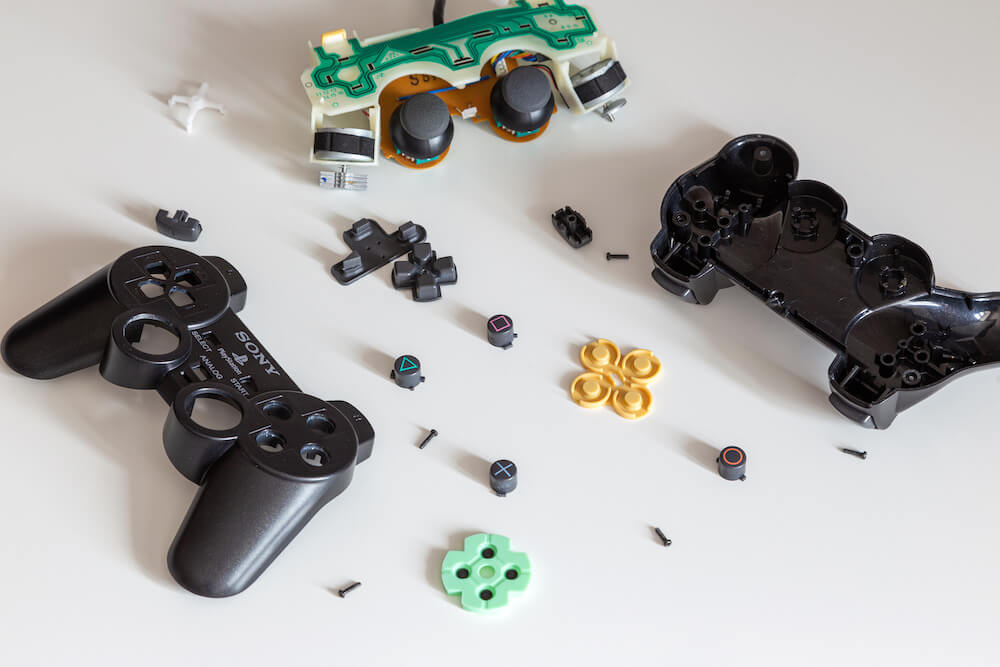
Materials Used to Injection Mold a Prototype Electronic Housing
Due to the harsh environment to which electronic components may be subjected, electronic housings must be robust. Typically, housings are created in metal. These metal housings can be created in many ways, typically by bending sheet metal, machining, or casting.
Injection molded electronic housings are much more cost-effective than metal housings and are often used for smaller, hand-held equipment applications. Plastic housings provide many advantages that metal housings do not:
- Cost-effectiveness: They are economical materials suitable for mass production, ensuring affordability for manufacturers and end-users.
- Durability: Plastics offer excellent durability, protecting electronic devices even in harsh environments. They are resistant to impact, chemicals, and temperature variations.
- Efficient manufacturing: Ease manufacturing with plastics leads to efficient production processes, reducing lead times and overall manufacturing costs.
- Versatility in design: Plastics’ moldability allows for creating complex shapes and intricate designs, providing versatility in housing design while maintaining structural integrity.
These characteristics make plastics ideal for electronic housing applications, ensuring reliable protection and cost-efficient production processes. The most common types of plastics used in electronic housings are listed below:
- Polycarbonate is known for its exceptional impact resistance, transparency, and thermal stability.
- ABS (Acrylonitrile Butadiene Styrene) balances strength, rigidity, and affordability, making it suitable for various applications.
- PVC (Polyvinyl Chloride) is valued for its versatility, chemical resistance, and ease of processing.
Advantages of Molding an Electronic Housing
Although 3D-printed prototypes offer visual design representation of the developing electronic housings, they cannot be used to assess performance and reliability. This limitation stems from the inability of 3D printing to precisely replicate the material properties and structural behavior found in final injection-molded housings. Injection molding, on the other hand, offers superior accuracy in replicating material composition, mechanical strength, and thermal properties essential for housing functionality.
Importance of Comprehensive Testing
During the design and development of electronic housings, physical testing of the housings must be performed to ensure that the housings will adequately perform to protect the electronics as intended. Beyond the fit and layout of the components within the housings, other types of testing must be considered:
- Thermal Testing: Evaluates how the housing withstands temperature fluctuations and extreme heat conditions, ensuring stability and functionality in different thermal environments.
- Stress Analysis: Assess the housing’s structural integrity by subjecting it to mechanical stress and determining resistance to deformation or breakage.
- Environmental Testing: Examines the housing’s ability to withstand moisture, humidity, and chemical exposure, ensuring functionality in diverse conditions
To achieve meaningful testing of electronic housings, injection molded prototype parts are preferred because they replicate the characteristics of mass-produced housing and ensure that the housings meet the required standards and specifications before advancing to mass production.
The Protoshop Way
Design for Manufacturability (DFM):
Protoshop employs a Design for Manufacturability (DFM) approach to ensure that electronic housing designs are optimized for efficient and cost-effective manufacturing. This involves carefully evaluating designs to identify opportunities for streamlining production processes and reducing manufacturing costs.
Moldability Review:
Our process includes a detailed moldability review to assess electronic housing designs’ suitability for injection molding. This thorough examination ensures that designs are moldable and can be efficiently produced using our advanced injection molding processes, minimizing the risk of manufacturing issues.
Rapid Injection Molding Tools:
At Protoshop, we fabricate high-quality prototype injection molding tools to expedite the development and reduce time-to-market for electronic housing prototypes. This approach lets us quickly create prototype molds, facilitating design and development adjustments before full-scale production manufacturing begins.
Quality Assurance and Testing:
We uphold rigorous quality assurance procedures to ensure that electronic housing prototypes meet industry standards and client specifications. We produce prototypes that facilitate functional testing, verification, and process validation of the housings early in the design phase, all conducted before commissioning expensive production tools. This thorough approach guarantees that the electronic housing prototypes are production equivalent and of the highest quality.
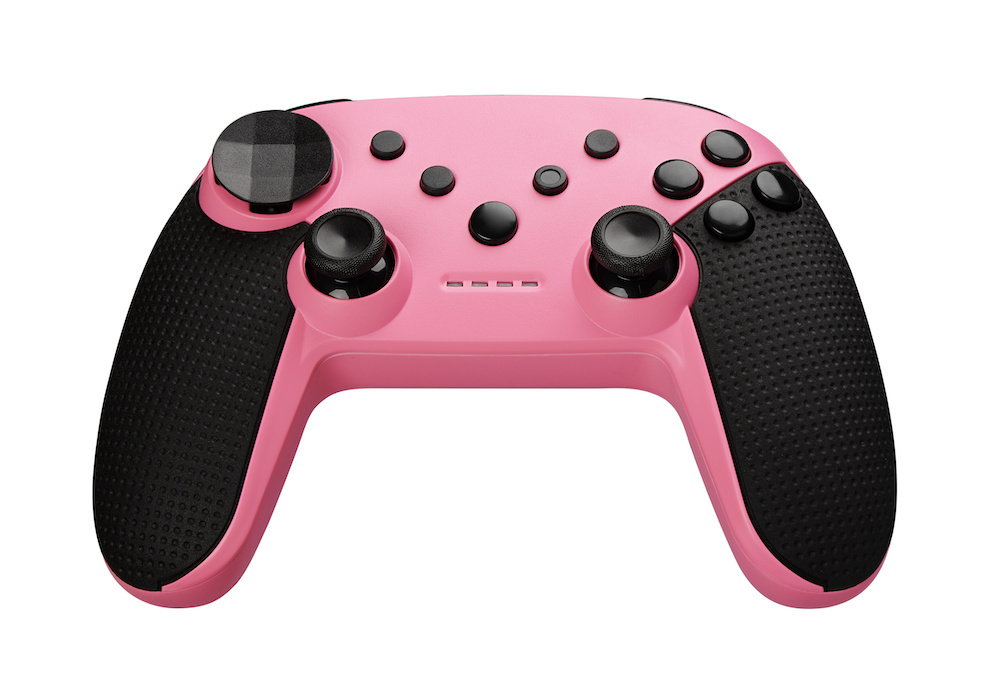
Considering Insert Molding Fasteners for Electronic Housings
Housings must be assembled in a way that the electronic components are enclosed securely. When the enclosure will not be opened again, this can be done with snaps, heat staking, or thread-forming screws for plastic. If the parts must be able to be disassembled repeatedly, such as to replace parts during maintenance or to replace batteries, metal fasteners are preferred.
These metal fasteners, such as metal posts, screw threads, or screws, can be integrated into the housing during injection molding through insert molding, providing reliable attachment points for electronic components such as circuit boards and connectors. Securely fastening components within the housing helps prevent issues such as loose connections, component movement, and potential damage during operation.
Connect with Protoshop Inc. for Your Complex Electronics Housing Prototype Project
With extensive expertise in electronic housing prototyping, we are committed to providing top-notch services and customer satisfaction. Contact us if you require housing prototypes or have inquiries about our capabilities.
We look forward to partnering with you and delivering exceptional results for your electronic housing projects, leveraging our state-of-the-art facilities and experienced team to meet your exact specifications and exceed your expectations.
Part Information & Lead Time
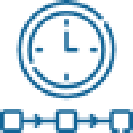
Lead Time
Typically, in 1 week, we will indicate the lead time when we provide your quote.

Maximum Molded Part Size
Part may be up to 8″ x 6″ x4″ (200 x 150 x 100 mm)
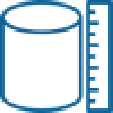
Maximum Part Volume
Shot volume up to 6 oz (170 g)
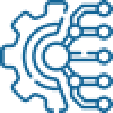
Tolerance
Typically <0.004″ (0.1 mm).
Tolerance of 0.001″ (0.025 mm) is possible with certain materials and part geometry. Let’s discuss your application.
Contact Protoshop Today
For exceptional prototype manufacturing solutions, reach out to Protoshop. Our team is equipped to handle the complexities of your electronic injection molding projects, offering tailored support and innovative solutions. Protoshop is not just a prototype parts supplier but is a development partner and provides expertise to accelerate your product development.
Contact us at help@protoshopinc.com or (888) 416-3334, or visit our website for detailed information. Partner with Protoshop for a seamless, quality-driven experience in medical component manufacturing.
Request a Quote