
Medical Prototype Injection Molding & Parts Manufacturing
Plastic Component Injection Molding for the Medical Industry
Protoshop Inc. stands at the forefront of medical component prototype injection molding, bringing over 15 years of medical-specific specialization in helping customers work through design issues with production-equivalent plastic components.
We are recognized for our comprehensive experience in prototype plastic part development for the medical industry using diverse materials tailored to medical industry needs.
Our approach combines the art and science of plastic part design for medical injection molding, guided by medical industry best practices and an in-depth understanding of material properties and design considerations.
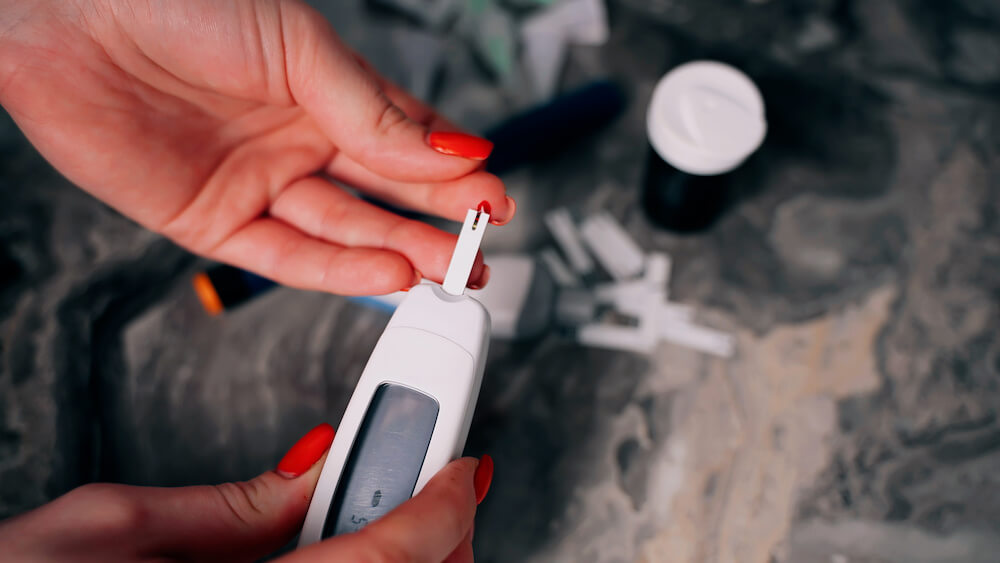
How Protoshop Excels
Protoshop sets itself apart from other prototype injection molding fab shops through a meticulous approach to prototype medical injection molding, emphasizing quality, precision, and flexibility at every stage. Specialized capabilities such as overmolding, insert molding, and expert machining makes Protoshop an ideal choice for medical parts requiring multiple materials or complex geometries.
Our extensive experience in diverse medical product applications, from surgical tools to IVD devices, allows Protoshop to tailor better molding solutions that avoid the pitfalls of less experienced prototype molders. We collaborate with the customer to find the fastest, least expensive way to create injection molded parts geared toward understanding critical design features and pursuing multiple design paths.
Protoshop’s Experience in Building Medical Components
At Protoshop, our experience spans an extensive range of medical projects, showcasing our proficiency in managing complex design requirements and production challenges. We emphasize the importance of integrating material selection early in the design process, allowing for accurate mold flow analysis and ensuring that the molded parts will meet engineering specifications
Medical Products Made with Prototype Injection Molding
Medical injection molding prototypes, during design and development activities, enable the efficient, high-volume production of critical plastic components for advanced medical products. Some examples include:
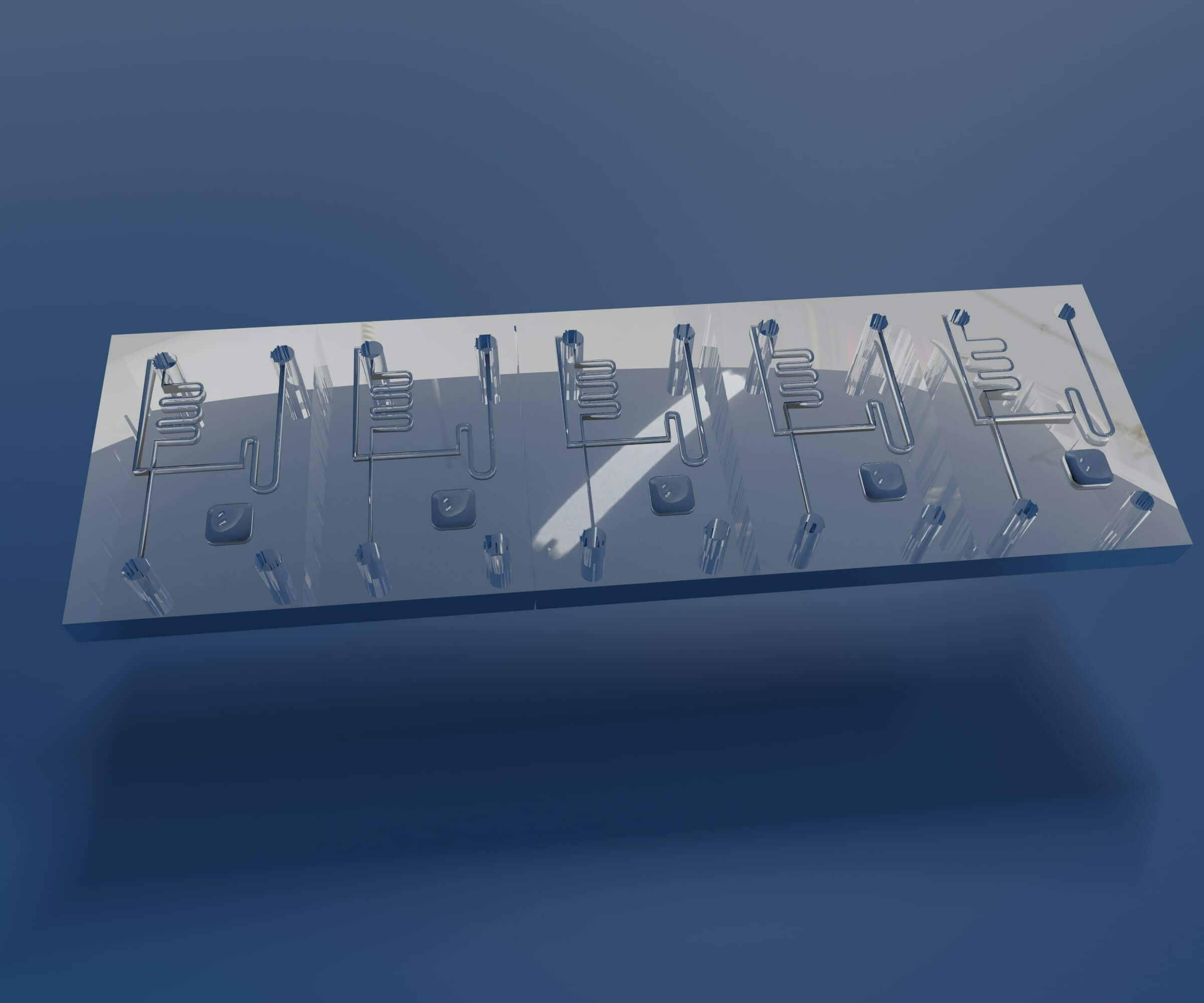
Device and Instrument Housings:
The external plastic casings encapsulating delicate internal electronics require precision dimensional tolerances that are only achievable through injection molding. Prototype molds yield higher quantities of prototypes at an affordable price and can be used to tweak the fit of all components before committing to production molds.
In Vitro Diagnostic (IVD) Devices:
Diagnostic devices must be molded with inert materials to prevent the plastic from leaching into the assays. Development of these medical devices necessitates injection molding parts during testing and clinical trials to verify repeatability of assay results before high-volume production molds are produced.
Drug Delivery Systems:
From EpiPens to insulin pumps, injection molded plastic parts comprise the containment and delivery mechanisms, allowing controlled medication dosing. These critical features must be tested using production-equivalent parts and are prime candidates for prototype molding.
Diagnostic Equipment:
Test devices and lab automation tools depend on the tight tolerances and reliable reproducibility offered by injection molded plastic components. Prototype parts produced through medical injection molding ensure the systems function as intended before the products hit the market.
Surgical Tools:
Scissors, clamps, forceps, and other instruments leverage injection molding to enable integrated features and ergonomic designs, boosting functionality. Production-equivalent plastic parts must be manufactured in clinical trials to fulfill product validation requirements. Prototype tooling can be used as production tools are being built.
With the capabilities to create tiny, complex, or multi-material components, injection-molded plastics are intrinsic to most cutting-edge medical product development. Our expertise in prototyping these intricate parts powers quicker innovation for clients worldwide.
Why Choose Us for Custom Injection Molding
Protoshop excels in rapid prototype injection molding, significantly accelerating product development timelines. Our integrated mold fabrication and medical injection molding capabilities within our California facility enable us to adapt to design changes and expedite the prototyping process swiftly. With the capacity to fabricate injection molds in just one week and deliver the first plastic parts within 1-3 days post-mold completion, we offer unparalleled speed and agility in the medical industry. This means part revisions happen quickly, surprises are avoided, and iterative timelines are shortened.
Our Commitment to Quality and Precision
Our commitment to quality and precision is evident in our use of durable tooling capable of 10,000+ cycles, ensuring dimensional accuracy and consistency. We provide thorough first-article inspections, demonstrating our adherence to the highest fit, form, and function standards. Protoshop’s customer-focused approach includes comprehensive design for molding analysis, material selection guidance, and ongoing partnership post-delivery, catering to intricate molds and low-volume production needs.
Case Study – In Vitro Diagnostic (IVD) Cartridge
In a collaborative effort to innovate In Vitro Diagnostic (IVD) cartridge design, our customer aimed to replace conventional assembly methods with a novel snap-together valving feature to control fluid flow efficiently. Our team engaged in developing and molding a prototype to ensure the precision and reliability of the valve assembly. After initial prototypes exhibited variability, we quickly adapted the mold design, achieving a successful snap-fit valve assembly with minimal cost on the second iteration.
Protoshop’s rapid prototyping capabilities proved critical in de-risking the innovative features of the product, allowing the integration of specific material properties and functional requirements essential for the IVD cartridge.
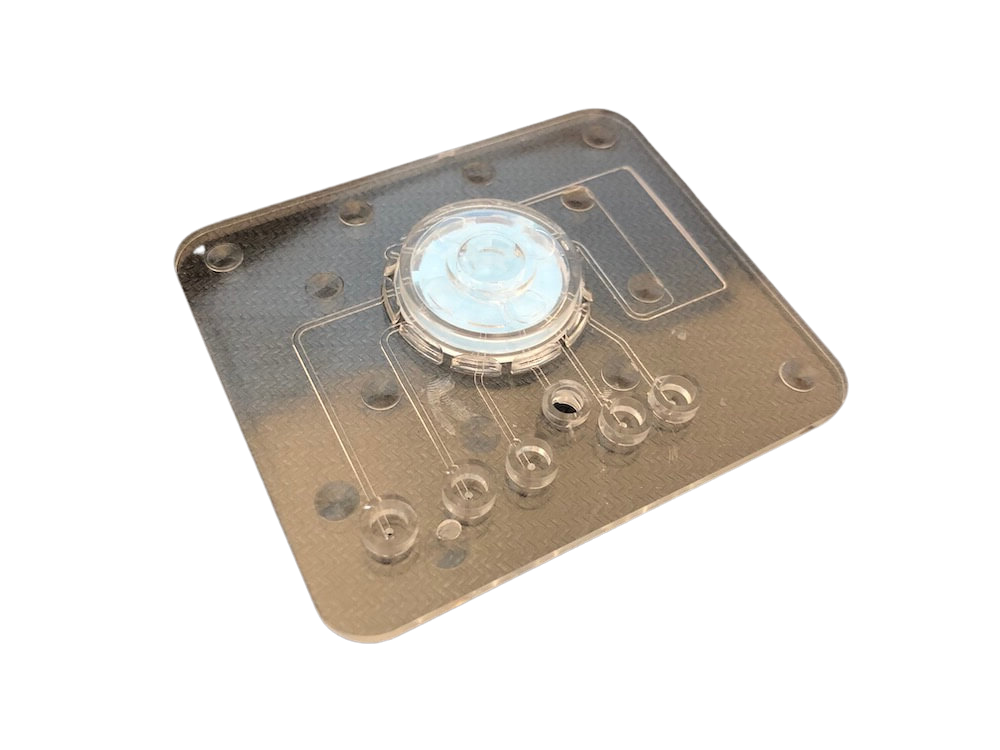
Part Information & Lead Time
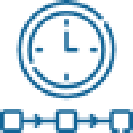
Lead Time
Typically, in 1 week, we will indicate the lead time when we provide your quote.

Maximum Molded Part Size
Part may be up to 8″ x 6″ x4″ (200 x 150 x 100 mm)
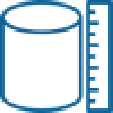
Maximum Part Volume
Shot volume up to 6 oz (170 g)
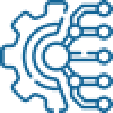
Tolerance
Typically <0.004″ (0.1 mm).
Tolerance of 0.001″ (0.025 mm) is possible with certain materials and part geometry. Let’s discuss your application.
Contact Protoshop Today
For exceptional prototype medical component manufacturing solutions, reach out to Protoshop. Our team is equipped to handle the complexities of your medical injection molding projects, offering tailored support and innovative solutions. Protoshop is not just a prototype parts supplier but is a development partner and provides expertise to accelerate your product development.
Contact us at help@protoshopinc.com or (888) 416-3334, or visit our website for detailed information. Partner with Protoshop for a seamless, quality-driven experience in medical component manufacturing.
Request a Quote