
Prototype Injection Molding
What is Plastic Prototype Injection Molding?
Plastic injection molding is the process used to create the plastic parts that are used in most of the products you use every day. Plastics are used in a wide range of applications, from simple buttons to complex implantable medical devices visible under x-ray and everything in between. This is why plastic resin manufacturers offer over 60,000 grades of plastic. Plastics are well suited for manufacturing due to their relatively low cost per part, part consistency, and ability to fabricate large numbers of parts quickly.
The basic principle of prototype injection molding hasn’t changed substantially since it was first patented in 1872. Over the last 150 years, innovations have involved the addition of electronic control and automation of the molding process. Plastic prototype injection molding consists of two essential parts: an injection unit and a clamping unit. The injection unit is where the plastic resin is added to the machine, and heat is applied to change the plastic resin to a flowable liquid state. The clamping unit contains the mold.
The mold is a machined assembly that contains the part detail to be molded. Once the mold is split into two sections, it allows the clamping unit to open and close the mold as needed. In order to mold a part, the clamping unit closes the mold, and the injection unit pushes the liquid plastic into the mold. The plastic quickly cools. The clamping unit opens the mold, and the part is ejected. The process then repeats.
Request More Information
Injection Molding Process
When developing a new product, it is typically necessary to fabricate a prototype injection mold to perform functional testing of the product. There are a couple of key reasons engineers utilize prototype injection molding rather than production molds. A production mold typically takes 2-3 months to fabricate. It would be a very long time to wait for molded parts. Prototype injection molds can be fabricated in as little as one week, allowing engineers to proceed more quickly with testing.
Typically, engineers discover during testing that their part design needs changes in order to meet product requirements. In that case, a mold iteration is needed. Prototype molds are faster and easier to iterate due to the softer metals that are used. Iterations are typically completed within a few days. Production molds are made out of hard steel. While mold iterations are possible in production molds, they tend to affect the mold’s life negatively. Ideally, the part design is finalized when the production mold is fabricated, and no iterations are needed. This allows the production mold to meet the full life cycle and optimize the investment.

What Types of Materials are Used in Injection Molding Prototypes?
Materials that are compatible with plastic prototype injection molding are known as thermoplastics. Within thermoplastics, there are approximately 70 different types. Commonly known types include polycarbonate, polypropylene, nylon, etc. Each thermoplastic type has a set of unique characteristics and usage scenarios that distinguish it from other types. Material selection for a part can be challenging because the engineer must be familiar with the 70 different types and know which type to select for the particular application.
For example, polycarbonate would be an ideal type to select if a part requires transparency and high strength. Once the type is selected, the next step would be to select a particular grade of material. Websites such as matweb.com and ulprospector.com are helpful plastic resin databases that make it possible to select a particular grade.
Continuing to use the polycarbonate example previously discussed, we find that there are over 6,000 grades of polycarbonate available. Selection of a particular grade requires a review of the part design and its product requirements, such as mechanical, cost, tolerances, environmental conditions, assembly, sterilization, regulatory, aesthetics, and any special requirements.
For example, this polycarbonate part may be a relatively thin wall part requiring a high melt flow grade. It could also be a medical part requiring gamma sterilization, requiring an additive to prevent color shift. These requirements can be searched on matweb.com and ulprospector.com to compile a list of the grades that meet those requirements. The final step would be to contact the distributors of those material grades for pricing and availability then place an order for the selected grade of polycarbonate.
Arburg Injection Molding Machines
Protoshop uses only Arburg production injection molding machines, a high-quality brand built in Lossburg, Germany commonly used in production injection molding. Our goal is to replicate production molding as closely as possible and using a production quality injection molding machine is critical. Testing and development using a high quality prototype part that closely replicates production makes transfer to manufacturing an exercise rather than a step involving risk.
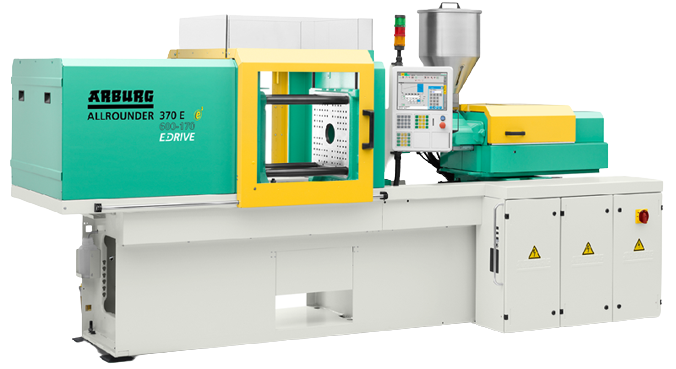
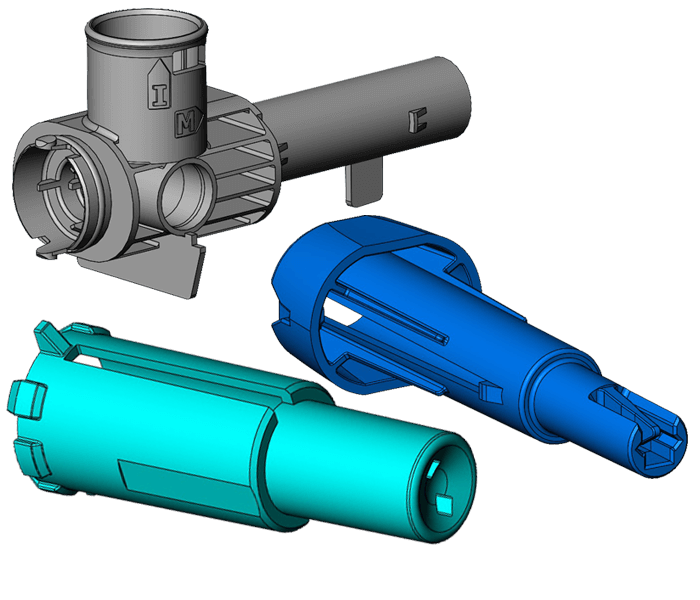
Prototype Molds with Complex Part Geometry are Our Specialty
We specialize in challenging molding applications. We have successfully designed and fabricated thousands of prototypes and don’t reject complex part geometry like other prototype molders. If a part is moldable, we can do it.
Injection Molding Prototype Part Information & Lead Time
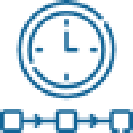
Lead Time
Typically 1 week, we will indicate the lead time when we provide your quote.

Maximum Part Size
Part may be up to 8″ x 6″ x4″ (200 x 150 x 100 mm)
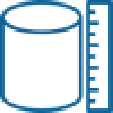
Maximum Part Volume
Shot volume up to 6 oz (170 g)
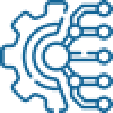
Tolerance
Typically <0.004″ (0.1 mm).
Tolerance of 0.001″ (0.025 mm) is possible with certain materials and part geometry. Let’s discuss your application.
Hear From Our Satisfied Customers
Prototype Injection Molding FAQS
Why Should You Consider Prototype Injection Molding During Product Design?
Utilizing prototype injection molded components offers distinct advantages in product design. While rapid prototypes and machined parts play a crucial role, they might not always mirror the mechanical attributes of injection molded components due to material constraints and fabrication techniques. Creating prototype molds early on helps pinpoint and address potential design and material issues, ensuring a smoother product launch and ultimately saving money. Interestingly, the time and cost involved in crafting these injection molds can be comparable to that of rapid prototypes, but they offer enhanced testing potential since they are equivalent to production parts.
At What Stage in Product Design Is It Optimal to Employ Prototype Injection Molding?
Given our expertise in product design, we’re adept in determining the right moment for prototype injection molding. Before delving into prototype molding or mold making, it’s advisable to use rapid (3D printed) prototypes because they offer swift iterations at a lower cost. Rapid prototypes can typically demonstrate 80-90% of the mechanical functionality. However, in instances where these prototypes don’t capture the mechanical behavior of molded components accurately, it becomes essential to transition to prototype molds.
How Consistent is The Repeatability of Your Prototype Injection Molds?
Our commitment to precision is evident in the consistency of our prototype molds, and several factors contribute to this:
- Our machinists/mold makers have 20+ years of experience and are highly specialized in creating prototype molds.
- These are single-cavity prototype molds; there is no variability across multiple cavities.
- Our molds benefit from temperature regulation akin to production molds, enhancing repeatability.
- The environmentally controlled setting in which parts are molded further boosts consistency.
- We exclusively employ Arburg production molding machines, renowned for their top-tier quality and uniform molding cycles.
As a result, our molded parts typically achieve tolerances within 0.003” of nominal, depending on the material selected. For dimensions that require a strict 0.001” tolerance, we can plan ahead to adjust the prototype injection mold to meet this stringent requirement.