Meet Protoshop.
A Leader in Plastic Prototype Molding.
Request a Quote
Receive a personalized, free and detailed review of your part design, potential molding defect solutions, and expert material selection assistance.
Why Companies Choose To Work With Protoshop:
Mobility reviews provided in person via Zoom
Material selection assistance
Challenging part models accepted
Molds typically fabricated in 1 week
Parts typically molded within 1-2 days
Accurate parts that closely replicate production quality
First article inspections provided for every molding lot free of charge
Molds designed to facilitate rapid iterations, typically within 1 day
Non-metal safe changes accommodated
Several thousand parts may be quickly molded
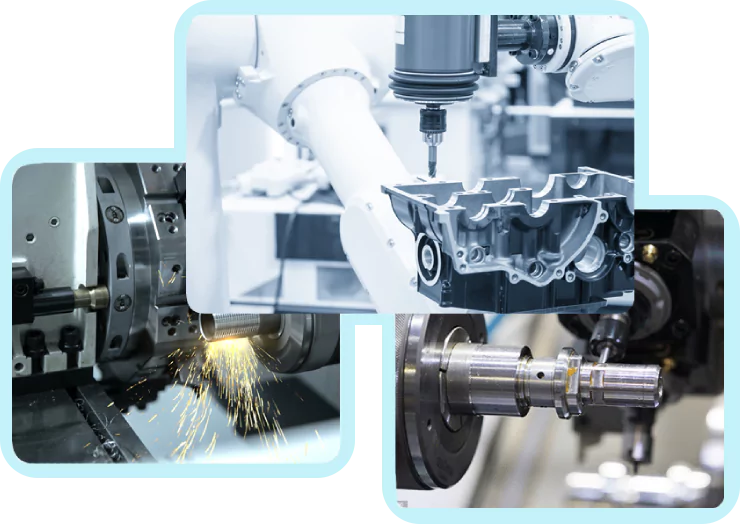
We excel in creating production-equivalent plastic components through our successful design and fabrication of thousands of prototype molds, all produced in-house. Unlike other prototype molders who may struggle with complex part geometries and reject them, we have the expertise and equipment to mold even the most challenging designs that push the boundaries of injection molding rules.
How Do We Do It?
Premium Prototype Molding Solutions
Professional Moldability Review
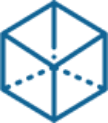
Unlike many prototype molders, we do not feel that an automated moldability review of your part model is sufficient. We prefer to provide a more personal and professional design review over Zoom with the goal of improving molded part quality while also minimizing cost and lead time. Clients can ask questions and fully understand our recommendations. The result of this collaboration is an improved part model ready for prototype molding that will meet your product requirements.
High-Quailty CNC Machine
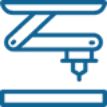
We invest in high quality CNC mills that are typically used to fabricate production molds. It’s overkill for prototype molds but necessary for achieving our goal of replicating production mold quality. The higher quality CNC mills also allow us to machine molds faster without sacrificing accuracy due to their improved spindle rigidity and cooling.
Superior Customer Experience
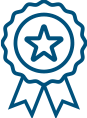
In addition to the personal moldability review we have invested in a website that significantly improves the prototype molding process for our customers. With our website you can get real time status updates, track shipping, order additional molded parts or mold iterations, and view the complete history of your projects including quotes, packing slips, and inspection reports.
Superior Molding Processing
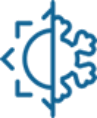
Our prototype molding system allows for both heating and cooling of the mold, similar to production molds. As a result, we’re able to create a molding process that yields significantly improved part quality. Critical dimensions are more accurate with tighter tolerances compared to other prototype molders
How The Process Works
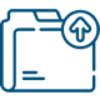
Upload part model for prototype mold quote
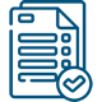
Accept quote

Mold fabrication completed

Mold sampling (25 ea) and client review
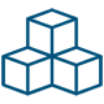
Order prototype parts as needed
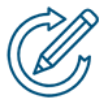
Request rapid mold iterations as needed
General Information
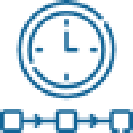
Lead Time
Typically 1 week, we will indicate the lead time when we provide your quote.

Maximum Part Size
Part may be up to 8″ x 6″ x4″ (200 x 150 x 100 mm)
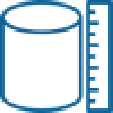
Maximum Part Volume
Shot volume up to 6 oz (170 g)
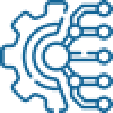
Tolerance
Typically <0.004″ (0.1 mm).
Tolerance of 0.001″ (0.025 mm) is possible with certain materials and part geometry. Let’s discuss your application.
Need Prototype Molds For Your Plastic Part?
The Prototype Injection Molding Process
Are you looking for high-quality plastic prototype molding? At Protoshop, we rapidly replicate mold quality to produce plastic prototypes for even the most complex specifications.
At Protoshop, we have exceptional versatility and the ability to produce a plastic prototype that meets your exact specifications.
• Our skilled Protoshop molders use their experience and expertise to create products of all shapes, sizes, and materials.
• We work closely with companies from various industries to ensure that our designs meet their exact needs, resulting in products of superior durability and excellent quality.
If you’re looking to propel your business to new heights, don’t hesitate to explore how plastic injection molding can benefit your company.
Protoshop can be a great resource if you need to design and produce plastic components using state-of-the-art plastic injection molding procedures. Our team is composed of skilled experts who have experience in engineering, design, mold fabrication, manufacturing, and management.
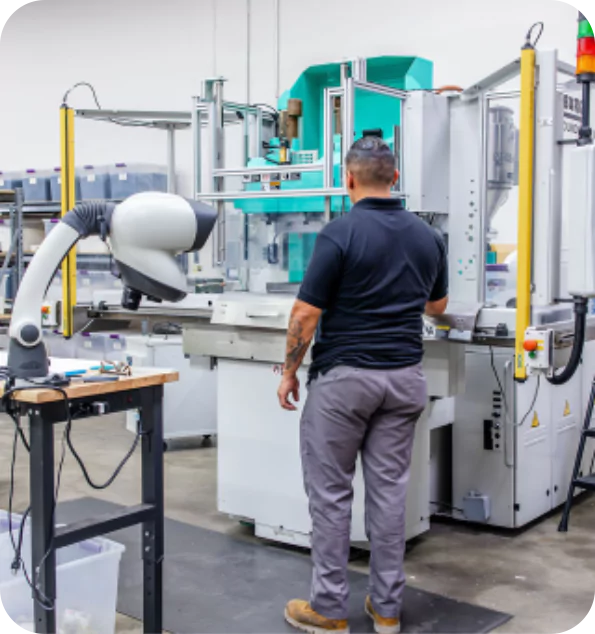
Rapidly Replicate Prototype Molds at the Highest Quality
We make all our molds using Arburg injection molding machines that are built in Lossburg, Germany. Our goal is to replicate production molding as closely as possible and using a production quality injection molding machine is critical.
Testing and development using a high quality prototype part that closely replicates production makes transfer to manufacturing an exercise rather than a step involving risk.
Hear From Our Satisfied Customers
Industries We Service:
Automotive
Consumer Electronics
Electronics Housings
Fluetic Manifolds
Gardening Devices
Housewares
Life Sciences
Biotech
Skin Care
Solar Panels
Toys
Wearable Tech
And Many More!
Our Trusted Partners
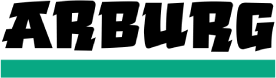
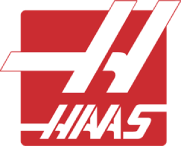

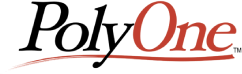
Proprietary Plastic Injection Prototype Molding Method.
Plastic injection molding is the process used to create the plastic parts that are used in most of the products you use every day. Plastics are used in a wide range of applications, from simple buttons to complex implantable medical devices visible under x-ray and everything in between. This is why plastic resin manufacturers offer over 60,000 grades of plastic. Plastics are well suited for manufacturing due to their relatively low cost per part, part consistency, and ability to fabricate large numbers of parts quickly.
The basic principle of injection molding hasn’t changed substantially since it was first patented in 1872. Over the last 150 years, innovations have involved the addition of electronic control and automation of the molding process. Our plastic prototyping service consists of two essential parts: an injection unit and a clamping unit. The injection unit is where the plastic resin is added to the machine, and heat is applied to change the plastic resin to a flowable liquid state. The clamping unit contains the mold.
The mold is a machined assembly that contains the part detail to be molded. Once the mold is split into two sections, it allows the clamping unit to open and close the mold as needed. In order to mold a part, the clamping unit closes the mold, and the injection unit pushes the liquid plastic into the mold. The plastic quickly cools. The clamping unit opens the mold, and the part is ejected. The process then repeats.