TABLE OF CONTENTS
- Material selection and shrinkage rate
- Molding machine
- Molding environment
- Mold fabrication equipment
- Cutting tool
The Challenge
A client approached us because they had not received acceptable parts with other prototype molding vendors. Issues included accuracy and surface finish of the 0.013” wide “teeth” features. We have extensive experience with micro-molding and molded similarly challenging features in the past, so we quoted mold fabrication and molding. There were three keys to success on this project: material selection, molding simulation and mold fabrication.
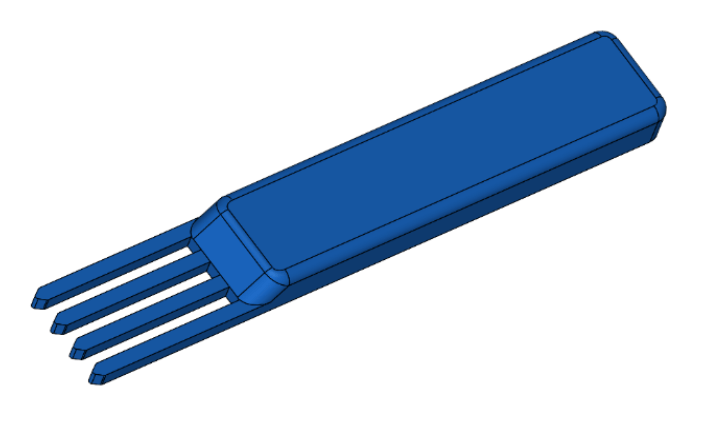
Material Selection
When we started Protoshop we wanted to provide a more complete customer solution than existing prototype molders. We found that other service providers assume that the customer has extensive experience in plastic part design and material selection. However, from our experience in medical product development, we knew that it takes many years and dozens of projects to achieve even basic proficiency in plastic design and material selection. Therefore, we created Protoshop with the goal that we are going to provide plastic part design and material selection assistance to better ensure that our customers yield parts that are going to be successful in their application.
In this case, the customer needed the “teeth” features to be very rigid yet would not easily fracture. We selected polycarbonate to be a good choice for this application. Polycarbonate is rigid yet does not easily fracture which meets their mechanical requirements. The shrinkage of polycarbonate is consistent and predictable, so it was a good choice for the accuracy requirements. There were two concerns about the use of polycarbonate. The first concern is that most grades of polycarbonate do not flow sufficiently to fill the “teeth” features. This was addressed by selecting a unique grade of polycarbonate with a high melt flow. The second concern was the high flow polycarbonate specification sheet which indicated the rigidity of the material would fall short of requirements. To address this concern, we had a small batch of high flow polycarbonate quickly compounded with 10% glass beads. The glass beads add substantial rigidity to the material and the low fill percentage did not significantly affect flow performance. With the material selected it was then time to proceed with molding simulation.
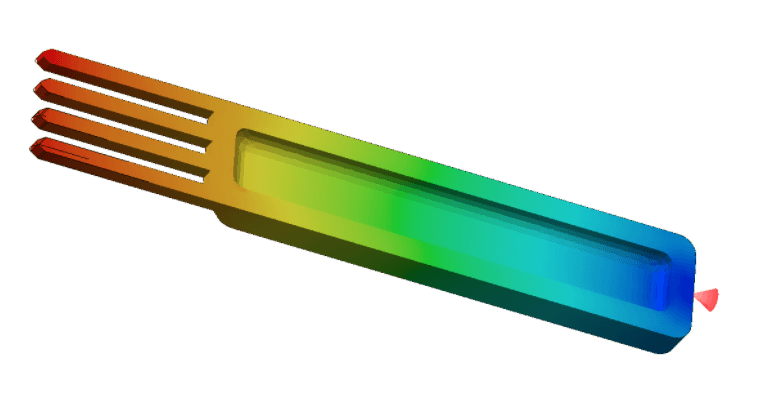
Molding Simulation
Solidworks offers an add-on software called “Plastics” which allows us to accurately simulate cavity filling during molding after entering a few key parameters such as the material, gate location, gate size, temperature and injection parameters. Protoshop has invested in a seat of this software to better ensure successful parts for our clients. The purpose of this software is to utilize the molding simulation on plastic parts which include features or materials that we anticipate could have potential for issues such as incomplete fill, trapped air, part warping, sink, etc. We can experiment with changing features such gate location, gate geometry and wall thicknesses to determine which yields optimal results. A thorough analysis can be completed in less than an hour. In this case the goal of the molding simulation is to confirm that the use of high flow polycarbonate with 10% glass bead fill is capable to fully filling the “teeth” features.
We entered the material parameters into the software and ran the simulation. Results are shown in the image above which indicates the temperature profile of the part at the end of the fill. The “teeth” features would not appear complete if the simulation did not show sufficient pressure to fill the features. Therefore, this simulation confirmed our expectation that we would successfully fill this part with the careful selection of high flow polycarbonate as the base material. We proceeded with prototype mold design and fabrication.
Mold Fabrication and Molding
It’s the skill and experience of our master machinists that sets us apart. Over thousands of prototype molds, we were able to accomplish the smooth and accurate surfaces on the “teeth” required by the client that other prototype molders were unable to achieve. We use high quality Arburg injection molding machines which is a critical tool towards molding consistent parts. Also, unlike most prototype molders, our molds include both heating and cooling which allows us to mold parts that more closely replicate production quality parts. After molding, parts were tested in our Inspection Lab. All “teeth” and gaps between were measured to be within the 0.0005” tolerance. This mold was designed, fabricated, and molded in just two days. Our client was pleased with the results and gave us the following compliment that was so clever that we had to share it.
“I was an atheist my whole life but when Protoshop started on our project I was forced to believe in a higher power. They are true Gods of molding”.