The Challenge
Our customer was developing an In Vitro Diagnostic (IVD) cartridge that required assembling a valving component to the cartridge to control fluidic flow for the assay. Standard means for assembling these types of valves into disposable IVD cartridges includes fasteners, ultrasonic welding, laser welding, heat staking and other secondary processes. The goal for this customer was to design a valve retaining feature that could assemble the valve to the cartridge by simply snapping the components together.
The Collaboration
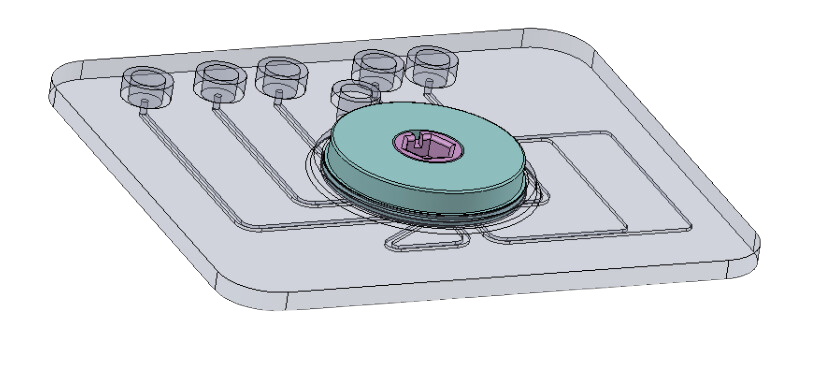
Once the part was designed, the customer came to us to mold prototypes to prove out the concept. If standard engineering tolerance stack-ups were used, there would be too much variability, and the valve would not seal reliably. Molded parts can shrink unpredictably post-molding depending on material selection and part geometry, but once the molding process is dialed in, molded part dimensions tend to be very consistent. Therefore, the customer created a critical function prototype of just the valve assembly, designing for minimum material conditions, after which Protoshop could fabricate the mold, mold parts and measure the critical snap feature geometry.
The Outcome
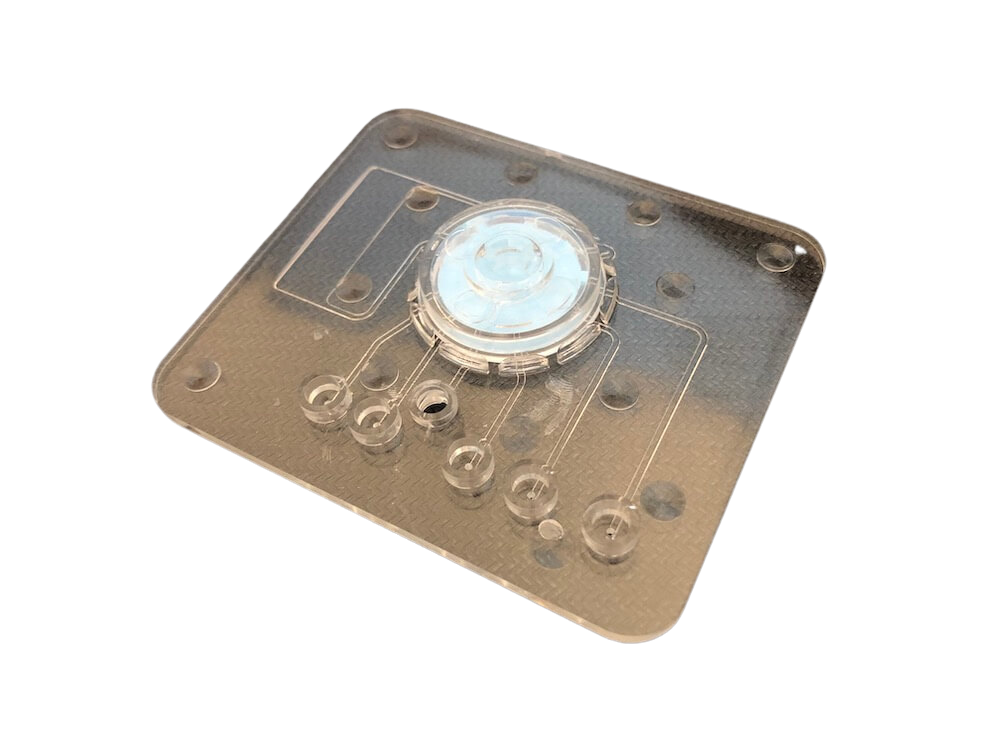
Protoshop fabricated 3 simple molds: the base chip with limited fluidic channels for testing the valve seal, the valve (substrate and overmold), and the retaining ring. After molding and measuring the parts, Protoshop made recommendations for tool changes to achieve the optimum fit of the snap features. The customer requested mold iteration, made metal-safe changes for a few hundred dollars, and molded the parts again. The second time was the charm, as the customer achieved the desired fit and valve function after just one iteration.
Fast Track the Solution
Innovation involves risk, and often, innovative features are not included in designs because of risks to timeline and budget. Those features can be isolated and tested independently in critical function prototypes. Examples of critical functions that can’t be fully tested with 3D printed prototypes may include snap features, rubber-like materials, parts that require overmolds or seals, parts that require functional testing of different materials, etc. At these critical product development design crossroads, prototype molds can be quickly fabricated to de-risk product features, and Protoshop is the development partner of choice for quick, high-quality, collaborative development using prototype injection molds.